CUMSA METHODOLOGY
quality and standardized concept
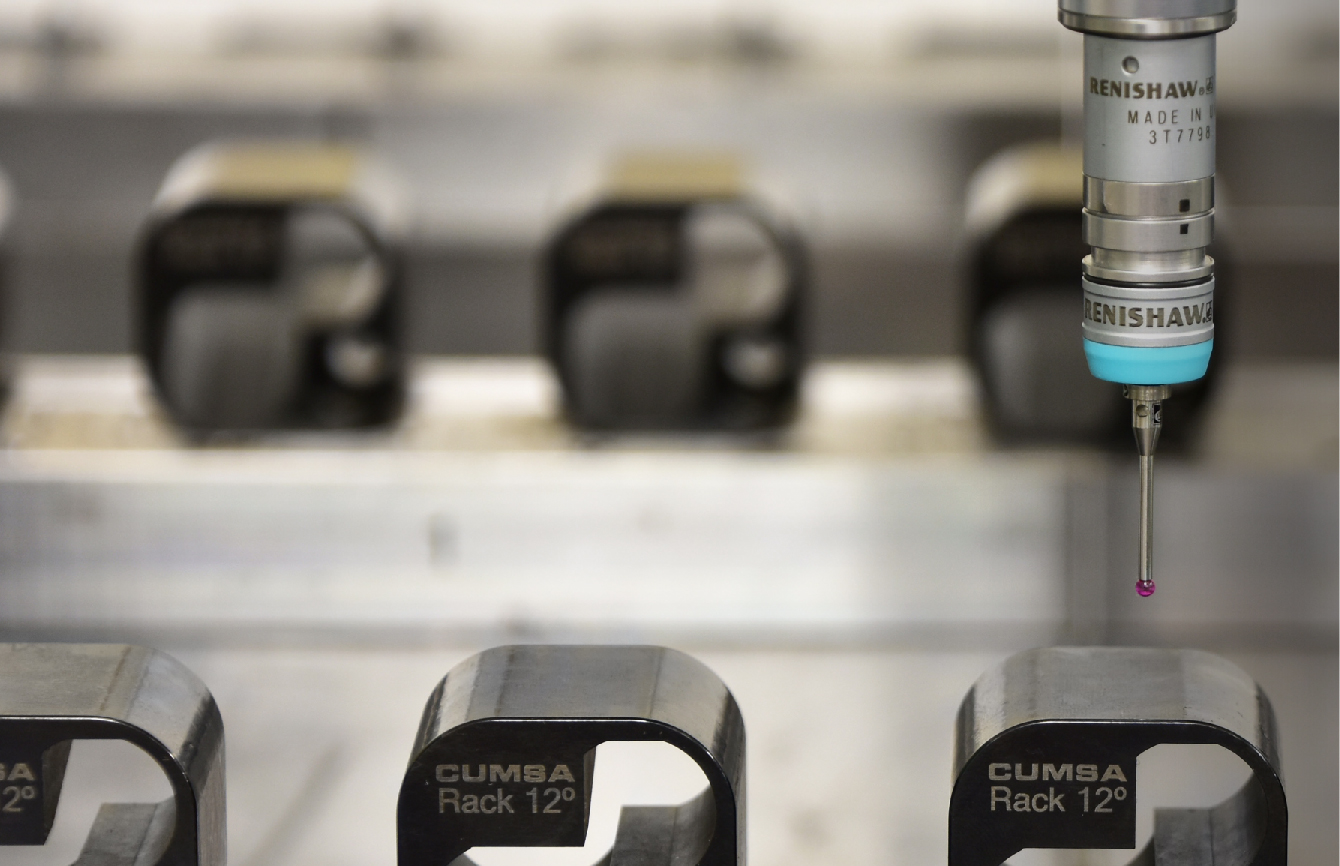
ABOUT
QUALITY MANAGEMENT
CUMSA's main objective is to respond to the needs of our customers with a high quality service and products. One of the pillars on which we are based, is a systematic process that allows us to continuously improve them, and we rely on ISO 9001 standards, with which we are certified since 1997, and annually we pass the corresponding audit of the system by a leading international company in the sector as Det Norske Veritas.
The three main areas of this quality system applied to our company are:
- · A constant application and investment in Information Technology, production and quality control systems, as well as in new machinery to optimize all processes.
- · Quality control throughout all production processes and all stages until the product is delivered to the customer. It is critical to ensure that the components of a product are interchangeable in case of need.
- · Continuous training of employees to increase know-how and quality related to products and services.
ABOUT
STANDARD PART CONCEPT
Standardized products are manufactured according to previously established parameters and measurements, which are defined in a published catalog. The use of standardized products offers the customer important competitive advantages:
- · Speed of cost calculation and planning.
- · Cost reduction.
- · Reduction of time in the manufacture of molds.
- · Reduction of mold size.
- · Fast adjustments of the components with the mold in the machine.
- · Minimization of production stops.
- · Quick replacement of parts.
The use of standard molds reduces the work of a moldmaker, saves between 30% and 40% of time in mold manufacturing, and consequently reduces the cost.
Another important advantage of the use of standard molds is the drastic reduction of production stoppages, since if a replacement is needed, it is in stock.